TDI is the short form for the toluene Di isocyanate. Loading, carrying, and discharging this cargo is not a child’s play. And there is a reason that I say this.
TDI reacts with moisture and water. It comes under cyanide group of cargoes and is highly toxic. It can ingest through the skin. And not the physical contact but even its vapors can ingest through the skin.
And after all these, TDI may require heating as its melting point is high. So many dangerous elements in one cargo and that’s why it is important to handle it carefully.
But in spite of being so dangerous, there are hardly any cargo-specific guidelines for carrying this cargo on ships. There are some extensive guidelines for handling TDI ashore but not for carrying onboard ships.
So I am hoping this guide can fill that gap. Let’s begin our voyage to carry TDI on board a chemical tanker. Let’s embark on a journey from loading and discharging a cargo of TDI.
Receiving Voyage orders
On receiving voyage orders to carry TDI onboard, the first thing to check is if we can carry this. By that I mean if the ship is designed to carry this cargo.
This is not only with TDI but every cargo loaded on chemical tanker needs to be checked if we can carry that.
To check this, take out the cargo list attached to the “certificate of fitness” of the ship. Certificate of fitness (COF) lists all the cargoes the vessel can carry. The name of the cargoes mentioned are the IMO names and are listed alphabetically.
Below is the section of the actual COF cargo list of a chemical tanker. As we can see Toluene Diisocynite is there on the list. So this chemical tanker can load TDI.
As we can see that on this ship, TDI can only be loaded in group A tanks and has some pre-conditions for loading TDI. While deciding if we can load TDI, we must satisfy these conditions.
Preparing a stowage plan for TDI
There are few things which the chief officer needs to keep in mind before he plans stowage for TDI cargo.
1) No water near to TDI cargo tanks
As TDI reacts with water, there cannot be any ballast adjacent to cargo tanks containing TDI. We need to check all stages of loading and unloading of each grade. We need to be sure that at no stage trim and list are so uncontrollable that we need to take ballast near to TDI tanks.
2) TDI stowed as far as possible from the accommodation area
We already discussed this. And we saw that as per COF, we can load TDI only in group A tanks. But even in group A, we should try to stow TDI as forward as possible. This is to avoid any exposure of TDI vapors inside the accommodation. Usually, we should try to stow TDI in tanks which are midship or forward of the midship.
3) No incompatible cargo to stow near to TDI
This is obvious but is worth mentioning. TDI comes under USCG compatibility group 12 and as such is not compatible with many cargoes. The stowage plan must ensure that we do not stow any of these incompatible cargoes adjacent to TDI.
Preparing for arrival load port
Before arriving at load port, you need to have made the following arrangements
1) Heating coils disconnected from the steam heating
Again as the TDI reacts with water, we cannot heat it with steam. Instead, a thermal oil heater is used for heating the cargo. Steam heating is the most common heating system onboard chemical tankers. In that case, the charterer will provide a portable thermal heater to heat the cargo, if required.
This heater’s pump is run by the ship’s hydraulic power pack. So connections from the main and return hydraulic line will be given to the portable heater pump.
Ship’s steam will heat the thermal oil. So connection from main and return line of the ship’s steam system will be connected to a portable heater.
Finally, the thermal oil outlet from the thermal heater will be connected to the tanks steam inlet line. From the return line of the tank, a hose will be connected to the thermal heater inlet into the thermal oil tank.
The idea is to heat the thermal oil with the ship’s steam and send this heated thermal oil into the cargo tank’s heating coil.
2) To blow heating coils with nitrogen
Before we connect the thermal oil heater with the tank coils, we need to blow the coils with nitrogen. This is to remove any traces of water as well as to remove moisture from the heating coils.
3) Ask for spill equipment
Handling the TDI spill requires certain chemicals. We need to make sure that we have these chemicals ready before we start loading.
Before the arrival loading port, make sure you have ordered all the materials required to handle TDI in the unfortunate event of any spill. Before loading starts, we need to have these chemicals mixed and kept standby.
4) Check no leak in the framo pump cofferdam
Well, this is routine for all the cargoes but it is even more important with TDI. The pump cofferdam should not be leaking. If it is leaking then we must renew the cargo seal (or Hydraulic seal) whichever is leaking.
5) Fill the pump cofferdam with DOP
With TDI inside the tank, we would not even allow the air (and moisture) to be inside the pump cofferdam. Yes, we need to be that particular about this cargo.
We need to first blow the cofferdam with nitrogen and then fill the cofferdam with a chemical called DOP.
To fill the cofferdam, we need to remove the air inlet and outlet pipes to the cofferdam located on the pump stack. We can then fill the DOP with a funnel. Continue filling DOP until we get DOP from the outlet of the purge pipe.
6) Have the antidote on board before loading
Well actually speaking there is no antidote for TDI exposure. Only the effects of exposure to TDI can be treated by the available antidote.
Before we can start loading, we must have this antidote for TDI available on board. If not already available onboard, We must request the antidote kit first thing after receiving the first voyage order. The antidote is only available in South Korea and a few other countries. So it would take some time to arrive in the US if you are loading TDI in the US.
7) Make sure dew point meter will be on board before loading
As TDI reacts with moisture, the tank will be purged with dry nitrogen to bring the dew point of the tank below -40 C.
But to measure the dew point, the vessel needs to have a dew point meter on board. The charterer will provide this meter but we need to make sure that arrangements are in place.
8) Test the tank for vapor tightness
This is one action that will take out much of your troubles during carriage of TDI to discharge port. And I must say even if vapor tightness was done a few months back, it will be worth doing it again for TDI tanks. You need to make sure that tanks can hold the pressure.
9) Make sure you have enough Nitrogen bottles
If your tanks are absolutely vapor tight, you would hardly need any nitrogen to fill in the tank. But we need to be ready for any unforeseen situations. Ideally, 10 Nitrogen bottles for one tank are considered enough. But if your tanks are not vapor tight, any amount of nitrogen may not be enough. That is why I stress that the vapor tightness of the tank is very important.
8) Train the crew
Finally, conduct a training session with the crew before arrival. Conduct the training session with particular reference to TDI. At the end of the training session, each crew must be able to answer at least the following questions
- Why TDI is dangerous?
- What action to take in case of a small spill like during hose disconnection
- What action to take in case of a major spill like overflow
- What action to take in case of fire
- What action to take if exposed to TDI vapors
- What action to take if in physical contact with TDI.
Hose connection/Disconnection will be done wearing a full chemical suit. So the training also needs to include wearing of a chemical suit and SCBA.
Particular emphasis to be made on the practice of shower under an emergency shower Before removing the chemical suit. This is to remove any traces of TDI from the suit and so to avoid exposure with TDI.
Oh well, you are ready to arrive at the load port.
Loading of TDI
Usually, TDI is loaded as a small parcel. Most of the time only in one or two tanks. It is advisable not to load TDI concurrent with any other operation including loading of other cargoes.
Before the loading operation can start, as I said tanks need to be purged to a dew point below -40 C. This is what we call drying of the tanks.
Hose connection has to be done after donning a full chemical suit and SCBA set. The loading rate needs to be as less as possible. Usually, TDI is loaded with loading rate of not more than 300 m3/Hr.
Sampling needs to be “closed sampling“. In spite of “closed sampling”, persons involved in sampling need to be in a chemical suit and SCBA set.
Because of high toxicity, Manifold samples are not allowed for TDI cargo. However, this sometimes could be allowed on case to case basis. You must follow the company manual about your company requirements for sampling of toxic cargoes. You can seek clarification from the company for if manifold samples need to be taken for TDI cargo.
Carrying TDI to discharge port
The only issue you need to be worried about during the voyage is the vapor tightness. Of course, you also need to measure the dew point daily. But if the tanks are vapor tight, you would not need to worry about anything else.
If you are sure of the vapor tightness of the tank, you can be sure there will not be much trouble during your voyage. If your tanks are not able to maintain the nitrogen pressure on your voyage, there are few things you can do.
1) Find the source of the leak
And you would agree that there can be many sources. The pressure might be dropping from the Butterworth hatches, tank dome packing, or PV valves. It is possible that all these are contributing to a small extent to have a larger impact on pressure drop.
Anyway, you should never use the soap solution method to find the leak.
2) Arrest the source of leakage
If you think you have found some source of nitrogen leakage, you should try to correct it.
For example, if the leakage is from Butterworth and tank dome, you may try to tighten the covers.
if the leakage is from PV valves, there is hardly anything that can be done at this stage. Some companies fix rupture disks in PV valves of the TDI tank to avoid any leakage from PV valves.
These rupture disks are designed to rupture at PV valve lifting pressure (mostly 20 KPa). The PV valves have a metal to metal sealing. Over the period, these metal surfaces develop pittings, which allows the leakage. The rupture disks ensure better sealing and thus no leakage. These rupture disks are fitted temporarily for cargoes such as TDI.
If fitted, the rupture disks need to be “approved one” and suitable with the PV valve fitted onboard. Also, it is important to have a tell Tale Gauge also fitted between the rupture disk and the PV valve.
In any case, you need to have enough nitrogen bottles to top it up as the pressure goes down.
Discharging of TDI cargo
Discharging will be with a vapor return line. And as with all discharging operations with a vapor return line, you need to ensure that tank pressure is not too high or too low.
The stripping needs to be done with the nitrogen.
After the discharging is complete, you need to make arrangements for washing the tank with chemicals supplied by the shore. The process is similar to prewash but with two differences
i) Prewash is for MARPOL purpose and for prevention of pollutants into the sea. Cleaning of TDI tank with chemical is for better after cleaning of the tank as TDI is insoluble in water.
ii) Prewash is usually done with water whereas this cleaning is done with a chemical called PCE. TDI is soluble in this chemical and that is the reason for using this chemical.
The process of cleaning will be as follows
- Around 5 m3 of PCE is put into the tank through the manifold. The chemical is then recirculated for at least 30 minutes.
- If there are two TDI tanks, this solution can be transferred to the second tank.
- After recirculation, the chemical will be given back to the terminal.
- The process is repeated with a fresh stock of 5m3 chemical.
If you have fixed tank cleaning machines, the recirculation will be much easier. But if you need to lower a portable machine, every effort should be made to avoid crew exposure with the TDI vapors.
Tank cleaning of TDI tank
The tank cleaning after discharging TDI is then a routine chemical tanker operation. As you are aware that Miracle and Milbros are two very good software for tank cleaning guide.
For example for finding out how to clean the tanks after TDI, open Milbros software
Click on From/To cleaning and search/choose the present cargo as Toluene diisocyanate. Choose the next cargo and click on View Results.
This will give the tank cleaning procedure for cleaning the tanks that contained TDI.
The tank cleaning involves hot seawater wash for 2-3 hours and then rinsing with fresh water.
Preparation for Next cargo
Finally, after the TDI tanks are clean and you are ready to load the next cargo, there are few things that needs to complete.
- Flush thermal oil from the heating coils of the tank. For this, we can remove the inlet hose from the steam coil and blow nitrogen or air into the coils. Connect a hose to the outlet and take out the thermal oil into empty drums.
- Disconnect the Hydraulic system from the portable thermal oil heater.
- Purge the cofferdam to remove the DOP from the cofferdam. Person purging the cofferdam must be wearing a chemical suit during purging.
Conclusion
TDI is one of the most dangerous cargoes carried on the chemical tankers. Any exposure to TDI can have immediate or long term health complications. Apart from health complications, if TDI is not handled in the way it warrants, serious accidents can result. However if handled correctly and as per guidelines, TDI is just like any other chemical carried on chemical tankers.
Share this:
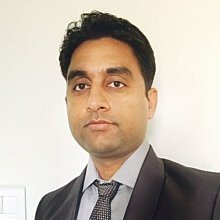
About Capt Rajeev Jassal
Capt. Rajeev Jassal has sailed for over 24 years mainly on crude oil, product and chemical tankers. He holds MBA in shipping & Logistics degree from London. He has done extensive research on quantitatively measuring Safety culture onboard and safety climate ashore which he believes is the most important element for safer shipping.
Search Blog
10 Comments


As always, your articles are very concise and helpful. Can you please name the antidote for this cargo? Also in general where to find the antidotes for any specific cargo when we receive orders , for eg:- Para Xylene.

Look Chris code of the cargo. There you 'll see which antidote

So nice blog,sir can you write on tank cleaning I;e polar jeet how and what all things should keep in mind b4 start cleaning by tank cleaning machine. Thanks in advance

Thanks for the write-up. It`s really a good read and also looks promising market. I went through a toluene diisocyanate market report at valuemarketresearch.com that evaluated the market across various segments. A deep dive into it might be profitable.

Good day Rajeev, could you please advise where I can find information regarding ballasting cargo tanks after carrying Undetectable Toxic cargoes, In our company this procedures followed like a rule but what is the publication they are refer to? Thanks a lot

Point missed...After loading the pump side discharge line to be blanked and Toluene to be filled from the manifold and bleeding at the pumpstack. Prior arrival this toulene require to be drained.
You are God-given gift Captain Rajeev, your unselfish sharing to us seafarers worldwide is unforgettable. Thank you so much. God Bless your family.

HI capt Rajeev , could you please advise the entry regarding cleaning of tank with pce is normal as we do with code E OR pre wash entry to be made
Leave Comment
More things to do on myseatime
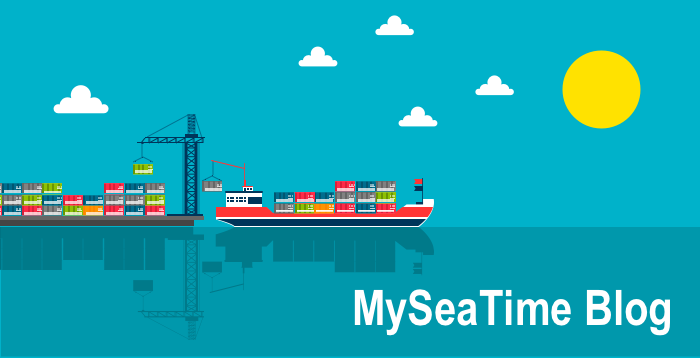
MySeaTime Blogs
Learn the difficult concepts of sailing described in a easy and story-telling way. These detailed and well researched articles provides value reading for all ranks.
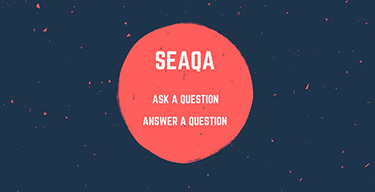
Seafarers Question Answers
Ask or answer a question on this forum. Knowledge dies if it remains in our head. Share your knowledge by writing answers to the question
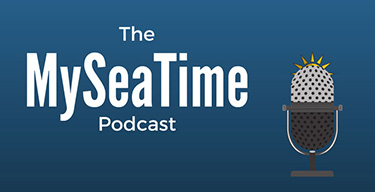
MySeaTime Podcast
This podcast on the maritime matters will provide value to the listeners. Short, crisp and full of value. Stay tuned for this section.
Nice article! Also to include that an exothermic reaction occurs when tdi reacts with neutralizer(ipa and nh3 mixture) resultant is a foam like substance. To avoid the additional cost of portable thermal oil heaters, a good operator will suggest u to load this cargo besides a heated cargo so that due to adjacent heat u can maintain its temperature!
Good points. Thanks for contributing.